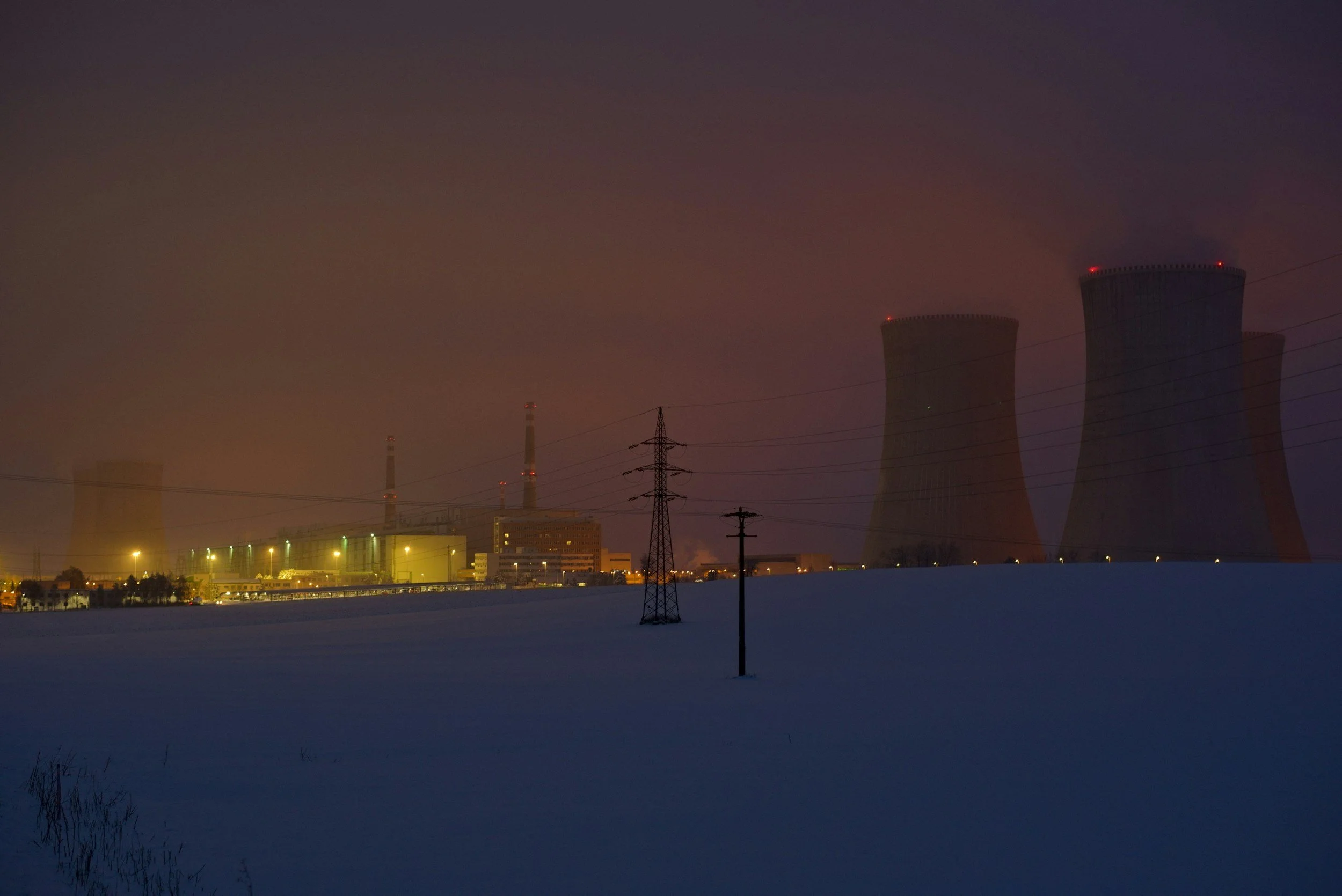
Nuclear energy
OMS provides inspection and measurement solutions to help clients in the nuclear industry overcome a range of challenges. Our systems use robotic crawler modules equipped with various OMS-developed acquisition hardware in conjunction with sophisticated software to identify and quantify surface defects that help our clients comply with relevant industry standards, and ultimately improve asset quality.
OMS has successfully operated key components from our inspection modules during Gamma radiation testing with a Cobalt 60 source and has qualified various acquisition and control hardware, including lasers, cameras, embedded controllers and drive motors. Our modular system design, with component overlap from 6” to 42” crawlers mean that this radiation testing has provided confidence that a large portion of OMS’s family of crawlers will operate successfully in a radiation environment.
Working in the nuclear industry has posed new challenges for the R&D team at OMS. Perhaps most notably is the development of a state-of-the-art inspection crawler capable of navigating DN50 (50 mm ID) pipe, with bends and T-sections. This system comprises a high-torque drive module with various other bolt-on modules including a front and rear facing camera module, high-resolution side camera module, laser surface measurement module, as well as other user-configurable modules to perform client-specific tasks.
OMS is an agile business with innovation at the heart of our approach. As three-time winners of the Queen’s Award for Innovation we have a wealth of experience developing innovative technology to help businesses in the nuclear industry overcome problems. We often work in partnership with our clients to build solutions that match their needs. For more information about what is possible contact us here.
Applications
Weld Checker-50
The OMS Weld Checker-50 tool is a prototype tool designed for the smallest pipe inspection offered by OMS and can be deployed into pipe sizes from 50 mm ID to 80 mm ID. This system was designed in flexible, modular portions because of the size constraints imposed by this size of pipe. It is equipped with a laser for accurate inner surface measurement, a side-facing camera with OMS designed LED lighting system and ten drive wheels to propel the module inside the pipe. Click here for a video of the propulsion system during testing phase at OMS offices.
AGILITY crawlers
Our AGILITY range of robotic crawlers are used in energy production operations throughout the world. Each crawler uses our award-winning AUGA.node inspection system which contains the laser and camera modules and can, depending on the support legs and drive system bolted on, deploy into pipe sizes ranging from 120mm to 60mm. The system can drive vertically and has been tested to pull up to 900N. As with all OMS crawlers, the Agility systems can be packaged into a standard peli-case for easy transportation.
Weld Checker – Modular
OMS created this system specifically for internal visual and laser inspection within the nuclear industry and is designed to bolt on to pre-existing third-party crawlers for those clients who prefer to use different systems. The modular scanning head uses the same common inspection components as the AGILITY system and has been subject to rigorous testing as part of its qualification to be used inside a steam generator in a nuclear power station.
Software:
At OMS easy-to-use and robust control software is a vital component of our inspection systems. Our software analyses data from numerous acquisition sources to provide a coherent and comprehensive analysis of a pipe’s interior. Our in-house software engineers continue to improve the software control, GUI and analysis and reporting features.
As standard, OMS control software provides the following on all crawler systems:
Real-time camera feedback (front, rear and side camera – if present)
Real-time distance tracking from wheels or tracks
Real-time laser data
Real-time system pitch and roll data
Control over lighting and image parameters
The analysis and reporting software provides, for example:
Automated weld feature analysis and reporting (i.e. concavity, root penetration, HiLo)
Overlaid camera and laser mapping data
Analysis of surface changes before and after a process – for example before and after grinding:
Material removed
Parent material removes
Remaining wall thickness
Output of scan data and images into a single MS Excel report for easy sharing and referencing after the scan